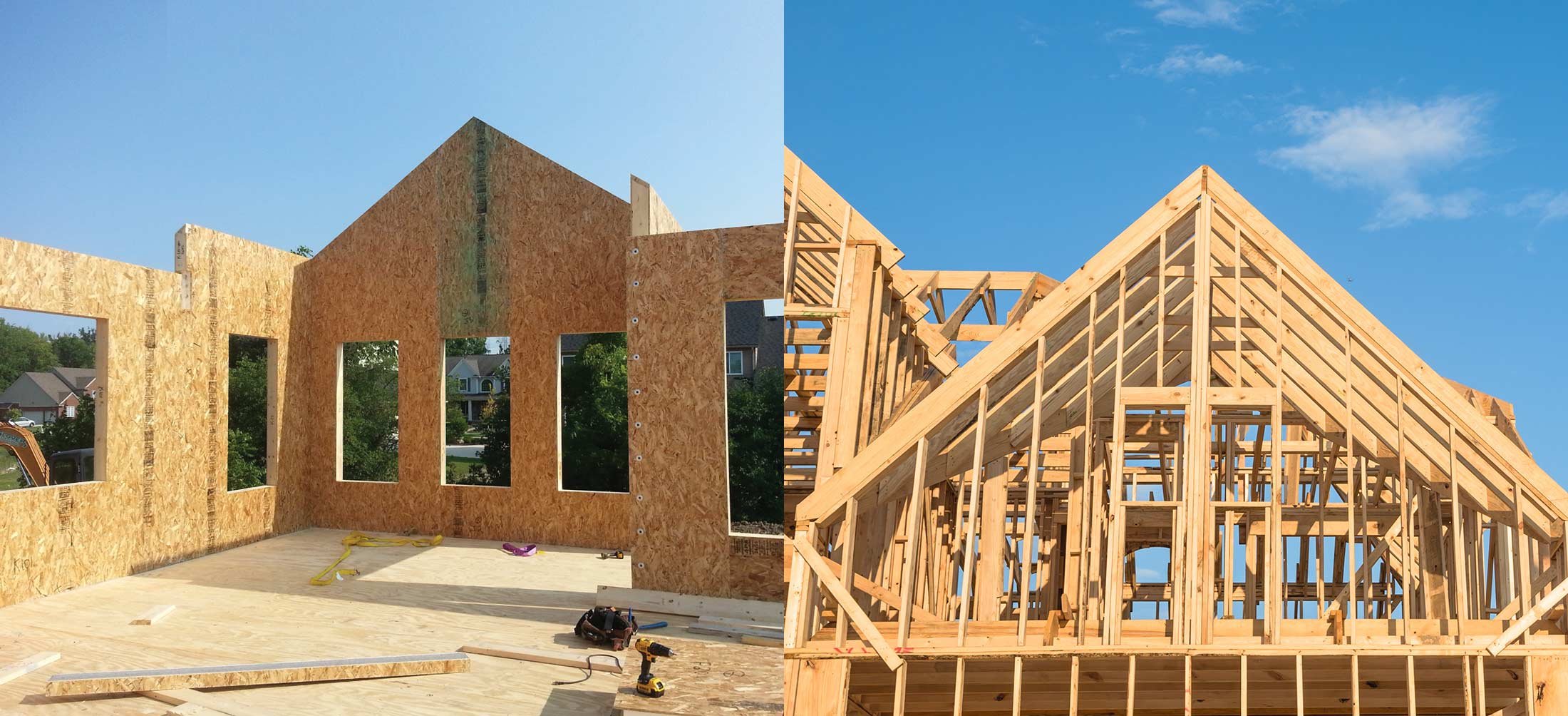
SIPS VS STICK
When comparing Structural Insulated Panels (SIPs) with traditional stick-frame construction, several factors affect cost, including material prices, labor, energy efficiency, and long-term savings. Below is a breakdown of these costs:
1. Material Costs
SIPs Construction
SIPs are pre-fabricated panels composed of a rigid foam insulation core sandwiched between two structural facings, typically oriented strand board (OSB).
Higher upfront material costs: SIPs are typically more expensive than traditional stick-frame materials. For example, SIPs cost approximately $7-$12 per square foot, depending on the manufacturer, size, and R-value (insulation value).
Less material waste: SIPs come pre-cut, reducing waste during construction.
Stick Frame Construction
Stick framing uses individual studs, insulation, sheathing, and siding, typically constructed on-site.
Lower material costs upfront: Stick framing typically costs around $4-$6 per square foot for materials like lumber and OSB.
More material waste: Because framing and cutting are done on-site, there tends to be more waste.
2. Labor Costs
SIPs Construction
Faster construction: SIPs arrive on-site pre-cut, reducing construction time by an estimated 40-60%. This results in lower labor costs.
Fewer skilled workers needed: Fewer people are needed to assemble SIPs because of their modular nature.
However, specialized labor may be required if the team isn't familiar with SIPs, leading to slightly higher costs for expertise.
Stick Frame Construction
Slower construction: Stick framing involves building the structure stud by stud, which increases labor time and costs.
More skilled workers required: Carpentry skills are essential for framing, and mistakes or inefficiencies can prolong construction.
Typically, labor accounts for around 40-60% of the total cost for stick framing.
3. Energy Efficiency
SIPs Construction
Superior insulation: SIPs typically have much higher insulation values (R-values) compared to standard stick framing, making them more energy-efficient.
Reduced air leakage: SIPs create a tighter building envelope, lowering heating and cooling costs by up to 50% over time.
This means lower energy bills in the long run.
Stick Frame Construction
Lower insulation value: Stick-framed walls are typically less energy-efficient due to thermal bridging (heat transfer through studs).
Higher long-term energy costs: A stick-framed home will likely have higher heating and cooling costs.
4. Construction Time
SIPs Construction
SIPs homes can be built in 30-50% less time compared to stick framing, reducing project timelines and associated costs such as site rentals and inspections.
Stick Frame Construction
Stick framing is a slower process, often taking longer due to the manual construction of each component on-site.
5. Long-term Maintenance and Durability
SIPs Construction
Durability: SIPs are highly durable, as the panels resist warping, twisting, and settling over time.
Less maintenance: The tight construction of SIPs means less wear and tear on heating and cooling systems and fewer long-term repairs.
Higher resale value: The energy efficiency and durability of SIP-built homes may result in higher resale values.
Stick Frame Construction
More potential for warping: Over time, wood studs in stick framing may warp, causing issues with insulation and structure.
Higher maintenance costs: Due to settling, shifting, and potential thermal bridging, stick-frame homes might need more maintenance over time.
6. Total Cost Comparison (Per Square Foot)
Material Costs
SIPS= $7 - $12/sq. ft.
STICK= $4 - $6/sq. ft.
Labor Costs
SIPS= Lower due to speed
STICK= Higher due to complexity
Energy Efficiency
SIPS= Superior, long-term savings
STICK= Lower, higher energy bills
Construction Time
SIPS= 30-50% less time
STICK= Longer, more labor-intensive
Long-term Costs (Maintenance)
SIPS= Lower due to durability
STICK= Higher due to repairs and energy
Total Project Cost (Rough)
SIPS= $9 - $14/sq. ft.
STICK= $6 - $9/sq. ft.
Initial Costs: SIPs construction typically has higher initial costs than stick-frame construction, mainly due to material prices. However, the reduction in labor time, combined with long-term energy savings, can make SIPs more cost-effective in the long run.
Energy Efficiency and Savings: If energy efficiency and long-term savings are key priorities, SIPs offer significant benefits over stick framing. For long-term homeowners, this can lead to overall cost savings.
Construction Speed: The shorter construction timeline with SIPs reduces overall labor and project costs, potentially offsetting the higher material costs.